Solid-State Batteries Progressing for Longer-Range EVs, But Is Outlook Too Rosy?Solid-State Batteries Progressing for Longer-Range EVs, But Is Outlook Too Rosy?
Solid-state batteries have advantages over traditional lithium-ion, and producers and automakers are making progress with production innovations to lower costs.
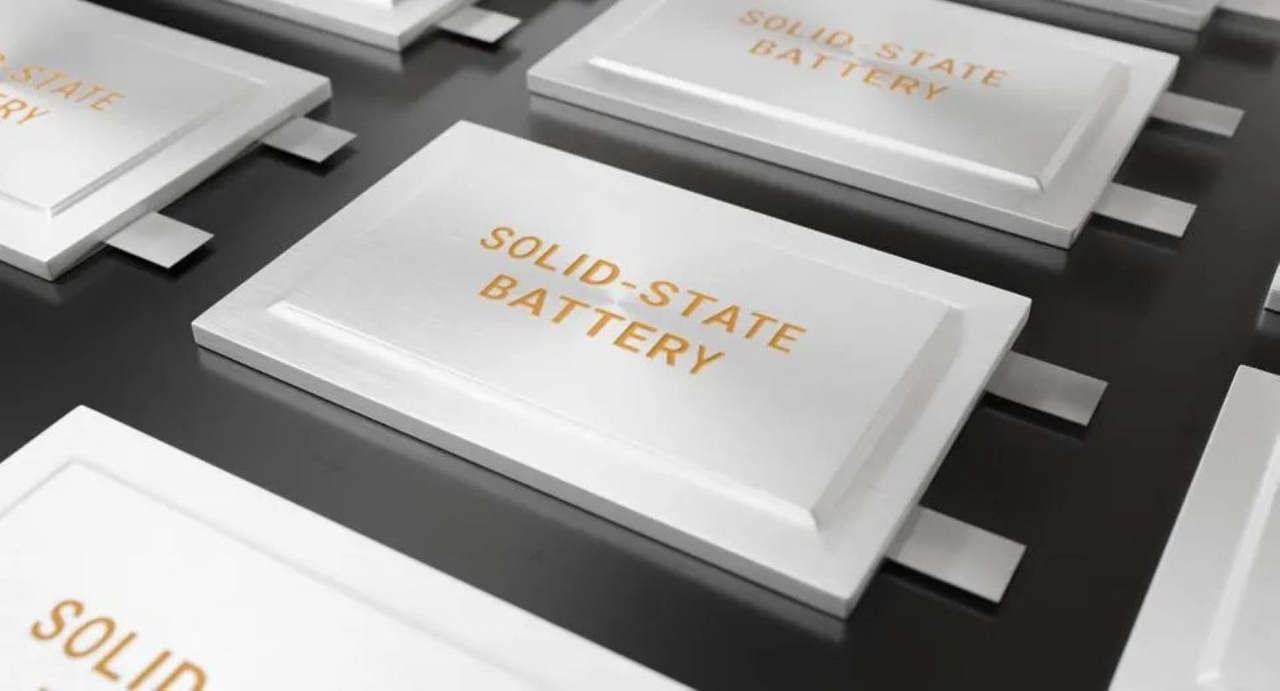
Solid-state battery (SSB) cells have several production and cost challenges to overcome to displace traditional lithium-ion technology, which is not as energy-dense. But legacy automakers planning to roll out battery-electric vehicles with SSB cells – with an electrolyte that is solid instead of liquid or gel as with traditional lithium-ions – say they are finding ways to overcome those issues and obstacles for the promise of eventual lower costs and longer range.
Toyota plans to introduce BEVs with SSBs between 2027 and 2028. Collaborating with Idemitsu Kosan to develop solid electrolytes essential for these batteries, Toyota and IK are developing sulfide-based solid selectrolytes, aiming for mass production by 2027. Idemitsu is constructing a lithium sulfide plant to support this initiative, targeting a production capacity sufficient for 50,000-60,000 EVs annually.
BMW aims to produce prototype SSB cells this year by 2025 and launch a single demonstration model. The German automaker is working with Solid Power to duplicate pilot production lines at BMW's facilities in Germany but has said mass production likely won’t occur until 2030.
Ford is testing full-scale SSB cells from Solid Power, with integration into future vehicles planned. Ford has invested in Solid Power and is collaborating on battery cell design and testing.
Nissan plans to launch BEVs equipped with all-SSBs by fiscal year 2028. It has opened a pilot plant at its Yokohama facility.
Hyundai is unveiled its all-solid-state EV battery pilot line in March, part of a $9 billion strategy to lead in next-generation EV technology, although recent executive comments suggest near-term uncertainty at the automaker for SSBs.
Stellantis plans to launch a demonstration fleet of EVs featuring SSBs by 2026, collaborating with Factorial Energy to develop these batteries.
Honda has established a 290,625-sq.-ft. (27,000-sq.-m) facility in Sakura City to streamline SSB production processes. The facility focuses on reducing manufacturing time and costs, with plans to commence battery production in January and aim for mass production in the latter half of the 2020s.
Through its collaboration with QuantumScape, Volkswagen is working on batteries that maintain capacity over extensive use, potentially allowing BEVs to travel more than 310,685 miles (500,000 km) without noticeable range loss.
Solid-state batteries have long been hailed as the future of electric vehicles, offering huge advantages over traditional lithium-ion chemistries using liquid or gel electrolytes. The challenges around SSBs, however, include difficulty in handling solid electrolytes; the thin films required are fragile, and scaling those processes with acceptable levels of discards remains tough. Factorial CEO Siyu Huang has described the journey as “production hell” in an interview with Inside EVs, marked by high scrap rates and material difficulties.
Stellantis and Factorial Energy, though, have validated a new semi-SSB cell that promises to get the industry closer to the objective. Stellantis says it will install these cells in a demonstration fleet of Dodge Charger Daytona BEVs starting in 2026.
Compared with conventional lithium-ion batteries, Factorial’s FEST (Factorial Electrolyte System Technology) solid-state tech promises significantly higher energy density, faster charging and longer driving range. And it claims it has overcome the production challenges that have bedeviled automakers and battery companies.
Factorial says these solid-state cells can still be 10 to 30 times more expensive than conventional lithium-ion cells, making scaled-up production still a few years away. The company’s batteries are polymer-based “semi-solid-state” batteries that stabilize the anode – a key area of degradation in traditional batteries – setting the stage for true all-SSBs in the future.
FEST cells have demonstrated an energy density of 375 Wh/kg and have undergone over 600 charging cycles, the company says, progressing toward automotive qualification – a milestone for large-format lithium-metal SSBs.
“FEST is a semi-solid electrolyte system. And there's nothing wrong with that because when it comes down to it, consumers don't really care what chemistry is in their battery,” says Wards Intelligence lead battery analyst Adam Ragozzino. “What consumers do care about is price, now more than ever, so any SSB is competing against relatively low prices for most traditional battery cells.”
Factorial has partnerships with other major automotive companies, including Mercedes-Benz and Hyundai, further validating their technology and accelerating its path to market.
Tal Sholklapper, CEO of battery quality control company Voltaiq, says he expects the first volume commitment to solid-state batteries will come with premium-priced BEVs so the higher prices can better be absorbed, and the smaller volumes allow for production learning curves. “But I do expect scaling up to happen after 2030.”
Listen to WardsAuto podcast with Tal Sholklapper.
China’s BYD and CATL, the dominant battery suppliers for the auto industry, also have noted 2030 is the most realistic timeframe for SSB introduction on a mass scale. The Chinese domestic new-vehicle market accounts for the largest share of battery-powered vehicles globally, with roughly 13 million of the 31 million new vehicles sold in China in 2024 being all-electric or plug-in hybrids, per the China Association of Automobile Manufacturers.
The cost issue is not insignificant. Lithium-ion costs are about $112/kWh (battery-pack level) as of spring 2025. SSBs are $400-$500/kWh in pilot stages (lab-scale). Production targets are to reach $100-$150/kWh by 2030 to be successful, according to FutureBatteryLab.
Early adopters like Stellantis, Hyundai, BMW and others are investing heavily to gain a technological lead with SSBs, betting on higher range, faster charging and reduced dependency on cobalt and nickel required in lithium-ion cells. While SSBs are currently three to five times more expensive to build, they could match or beat lithium-ion costs after 2030 if manufacturing and BEV volume mature.
The Payoff
SSBs can store more energy than traditional lithium-ion batteries. They enable longer driving ranges without increasing battery size or weight; estimates suggest 30% to 50% longer range compared to current lithium-ion packs.
Despite most U.S. drivers traveling less than 50 miles (80 km) per day, range anxiety remains a significant concern for potential battery-electric-vehicle (BEV) buyers. A recent study by Cox Automotive revealed that over 80% of consumers hesitated to embrace electric vehicles due to worries about range anxiety.
Other benefits to SSBs include their ability to handle much faster charge rates with lower risk of overheating. Charging times could drop dramatically – 15% to 80% in under 15-20 minutes, according to companies such as Factorial and Toyota. Solid electrolytes are less flammable than liquid electrolytes used in current batteries. Reduced risk of fires, thermal runaway or explosions is a key selling point for broader consumer adoption. SSBs degrade less over time, potentially doubling or tripling battery lifespan and lowering total cost of ownership for BEV customers.
Final production of BEVs is simpler and thus less costly too because SSBs they produce less heat during operation and charging, simplifying vehicle design and lowering BEV manufacturing costs in the long term.
There is a lot of work to do on SSBs at a time when market growth for BEVs seems uncertain. But there is little doubt that BEVs are going to remain a significant percentage of new-vehicle sales, so the work for better batteries continues.
About the Author
You May Also Like